Bearing
Bearing
"Bearing is a mechanical element which locates two machine part relative to each other & permit a relative motion between them."
It permits a relative motion between the contact surfaces of the members, while carrying the load. A little consideration will show that due to the relative motion between the contact surfaces, a certain amount of power is wasted in overcoming frictional resistance and if the rubbing surfaces are in direct contact, there will be rapid wear. In order to reduce frictional resistance and wear and in some cases to carry away the heat generated, a layer of fluid (known as lubricant) may be provided. The lubricant used to separate the journal and bearing is usually a mineral oil refined from petroleum, but vegetable oils, silicon oils, greases etc., may be used.
Parts of Bearing
The standard essential components of a ball bearing are defined as follows:
1. Inner Ring
The Inner Ring is the smaller of the two bearing rings. Inner ring has a groove on its outer diameter to form a pathway for the balls. The surface of outside diameter path is finished to extremely tight tolerances and is honed to a very smooth. The inner ring is mounted on the shaft and it is the rotating element.
2. Outer Ring
The Outer Ring is the larger of the two bearing rings. On outer ring there is a groove on its inside diameter to form a pathway for the balls. Outer ring surface also has the same high precision finish of the inner ring. The outer ring is usually held stationery.
3. Balls:
Balls of a bearing are the rolling elements that separate the inner ring and outer ring and permit the bearing to rotate with minimal friction. The radius of the ball is made slightly smaller than the grooved ball track on the inner and outer rings. This makes the balls to contact the rings at a single point. Ball dimensions are controlled to very high accuracy. Ball roundness, surface finish and size variations are important attributes. These attributes are controlled to a micro inch level.
4. Cage (Retainer):
The purpose of the cage in ball bearing is to separate the balls, maintaining constant spacing between the inner and outer rings, to accurately guide the balls in the path during rotation and to prevent the balls of bearing from falling out.
The purpose of the cage in ball bearing is to separate the balls, maintaining constant spacing between the inner and outer rings, to accurately guide the balls in the path during rotation and to prevent the balls of bearing from falling out.
5. Lubrication:
The lubricant is an integral part of a bearing’s standard components. Lubrication is added to reduce friction losses in bearing between inner and outer rings.
The lubricant is an integral part of a bearing’s standard components. Lubrication is added to reduce friction losses in bearing between inner and outer rings.
Other Optional Bearing components:
The other additional components shields and seals enhance the performance and life of the ball bearing. These optional components are added to the bearing as per the customer requirement to increase performance of ball bearing.
Shields:
The shield is a stamped, profiled sheet metal disc. Shield is pressed into a very small groove on the inside edge diameter of the outer ring. A small space or gap remains open between the outside diameter of the inner ring and shield. Because the shield does not contact the inner ring of the bearing, there is no added friction between the shield and bearing. This results in a bearing that has a very low torque. Purpose of shields is to keep larger particles of contamination from entering the bearing.
Seals:
The seal is also inserted into the very small groove on the inside, edge diameter of the outer ring. The inner edge of the seal is moulded into a specifically designed lip configuration.
The seal is also inserted into the very small groove on the inside, edge diameter of the outer ring. The inner edge of the seal is moulded into a specifically designed lip configuration.
Classification of Bearings
1. Depending upon the direction of load to be supported.
(a) Radial bearings, and (b) Thrust bearings.
2. Depending upon the nature of contact.
(a) Sliding contact bearings, and (b) Rolling contact bearings.
3. Depending upon the Materials
(a) Metallic Bearings and (b) Non Metallic Bearings
4. Depending upon the type of loading
(a)Bearing with Steady load and (b) Bearing with a variable or fluctuating load
1. Types of Sliding Contact Bearing
1. Depending upon the guided action
(i) Slipper or Guide Bearing
(ii) Journal or Sleeve bearings
2. Depending upon Angle of Contact
(i) Full Journal Bearing
(ii) Partial Journal Bearing
* The Full Journal Bearing & Partial Journal Bearing are again two types-
(i) Clearance Journal Bearing
(ii) Fitted Journal Bearing
3. Depending upon (length/diameter) Ratio
(i) Short Bearing
(ii) Long Bearing
(iii) Square Bearing
4. Depending upon Thickness of Layer of Lubricant
(i) Thick film or Hydrodynamic lubricated bearing
(ii) Thin film or Partial lubricated bearing
(iii) Zero film bearing
(iv) Hydrostatic or externally pressurized lubricated bearing
2. Types of Rolling Contact Bearing (Antifriction Bearings)
(1) Ball Bearing
(2) Roller Bearing
(1) Ball Bearing
(a) Radial Ball Bearing
(i) Single row deep groove bearing
(ii) Filling notch bearing
(iii) Angular contact bearing
(iv) Double row bearing
(v) Self-aligning bearing
(a) Externally self-aligning bearing, and (b) Internally self-aligning bearing.
* The Thrust Bearing also Classified-
(a) Marginally Lubricated Bearings
(b) Hydrodynamically Lubricated Bearings
(i) Tapered Land Bearing
(ii) Tilting Pad Bearing
(2) Roller Bearing
(a) Radial Roller Bearing
(i) Cylindrical roller bearings
(ii) Spherical roller bearings
(iii) Needle roller bearings
(iv) Tapered roller bearings
(b) Thrust Roller Bearing
Non-Metallic Bearings
(a) Rubber Bearings
(b) Wood Bearings
(c) Plastic Bearings
(d) Carbon-Graphite Bearings
(e) Glass Bearings
(f) Ceramics & cermets Bearings
Other Types of Bearings
1. Fluid Bearings
2. Magnetic Bearings
3. Jewel Bearings
1. Depending upon the direction of load to be supported.
(a) Radial Bearing-
In radial bearings, the load acts perpendicular to the direction of motion of the moving element.

(b) Thrust Bearing-
In thrust bearings, the load acts along the axis of rotation.

The Thrust ball bearings are two types.
(i) Step Ball Bearing
In a foot step or pivot bearing, the loaded shaft is vertical and the end of the shaft rests within the bearing.
(ii) Collar Ball Bearing
In case of collar bearing, the shaft continues through the bearing. The shaft may be vertical or horizontal with single collar or many collars.
2. Depending upon the nature of contact.
(a) Sliding Contact Bearing
In sliding contact bearings, the sliding takes place along the surfaces of contact between the moving element and the fixed element. The sliding contact bearings are also known as plain bearings.

1. Depending upon the guided action
(i) Slipper or Guide Bearing
The sliding contact bearings in which the sliding action is guided in a straight line and carrying radial loads, may be called slipper or guide bearings. Such type of bearings are usually found in cross-head of steam engines.
(ii) Journal Bearing or Sleeve Bearing
The sliding contact bearings in which the sliding action is along the circumference of a circle or an arc of a circle and carrying radial loads are known as journal or sleeve bearings.
2. Depending upon Angle of Contact
(i) Full Journal Bearing
When the angle of contact of the bearing with the journal is 360° then the bearing is called a full journal bearing. This type of bearing is commonly used in industrial machinery to accommodate bearing loads in any radial direction.
(ii) Partial Journal Bearing
When the angle of contact of the bearing with the journal is 120°, then the bearing is said to be partial journal bearing. This type of bearing has less friction than full journal bearing, but it can be used only where the load is always in one direction. The most common application of the partial journal bearings is found in rail road car axles.
* The Full Journal Bearing & Partial Journal Bearing are again two types-
(i) Clearance Bearing
If the diameter of the journal is less than that of bearing is called Clearance Bearing.
(ii) Fitted Bearing
When a partial journal bearing has no clearance i.e. the diameters of the journal and bearing are equal, then the bearing is called a fitted bearing.
3. Depending upon (length/diameter) Ratio
(i) Short Bearing
l/d is less than 1, then the bearing is known as short bearing.
(ii) Long Bearing
l/d is greater than 1, then the bearing is known as long bearing.
(iii) Square Bearing
l/d is equal to 1, then the bearing is known as square bearing.
4. Depending upon Thickness of Layer of Lubricant
(i) Thick film or Hydrodynamic lubricated bearing
The thick film bearings are those in which the working surfaces are completely separated from each other by the lubricant. Such type of bearings are also called as hydrodynamic lubricated bearings
(ii) Thin film or Partial lubricated bearing
The thin film bearings are those in which, although lubricant is present, the working surfaces partially contact each other at least part of the time. Such type of bearings are also called boundary lubricated bearings.
(iii) Zero film bearing
The zero film bearings are those which operate without any lubricant present.
(iv) Hydrostatic or externally pressurized lubricated bearing
The hydrostatic bearings are those which can support steady loads without any relative motion between the journal and the bearing. This is achieved by forcing externally pressurized lubricant between the members.
(b) Rolling Contact Bearing
In rolling contact bearings, the steel balls or rollers, are interposed between the moving and fixed elements. The balls offer rolling friction at two points for each ball or roller.
The ball and roller bearings consist of an inner race which is mounted on the shaft or journal and an outer race which is carried by the housing or casing. In between the inner and outer race, there are balls or rollers. A number of balls or rollers are used and these are held at proper distances by retainers so that they do not touch each other. The retainers are thin strips and is usually in two parts which are assembled after the balls have been properly spaced. The ball bearings are used for light loads and the roller bearings are used for heavier loads.
(1) Ball Bearing
(a) Radial Ball Bearing- When a ball bearing supports only a radial load, the plane of rotation of the ball is normal to the centerline of the bearing.

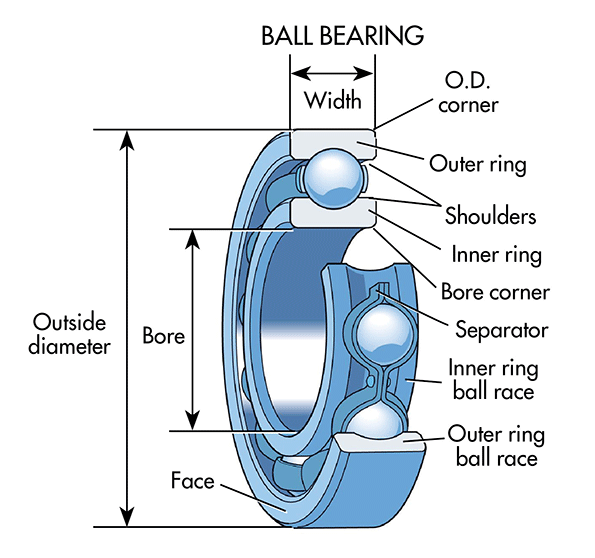
(i) Single row deep groove bearing
During assembly of this bearing, the races are offset and the maximum number of balls are placed between the races. The races are then centred and the balls are symmetrically located by the use of a retainer or cage. The deep groove ball bearings are used due to their high load carrying capacity and suitability for high running speeds. The load carrying capacity of a ball bearing is related to the size and number of the balls.


(ii) Filling notch bearing
These bearings have notches in the inner and outer races which permit more balls to be inserted than in a deep groove ball bearings. The notches do not extend to the bottom of the race way and therefore the balls inserted through the notches must be forced in position. Since this type of bearing contains larger number of balls than a corresponding unnotched one, therefore it has a larger bearing load capacity.


(iii) Angular contact bearing
These bearings have one side of the outer race cut away to permit the insertion of more balls than in a deep groove bearing but without having a notch cut into both races. This permits the bearing to carry a relatively large axial load in one direction while also carrying a relatively large radial load. The angular contact bearings are usually used in pairs so that thrust loads may be carried in either direction.

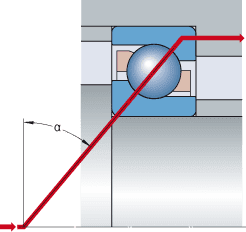
(iv) Double row bearing
These bearings may be made with radial or angular contact between the balls and races. The double row bearing is appreciably narrower than two single row bearings. The load capacity of such bearings is slightly less than twice that of a single row bearing.

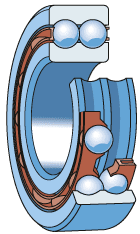
(v) Self-aligning bearing
These bearings permit shaft deflections within 2-3 degrees.
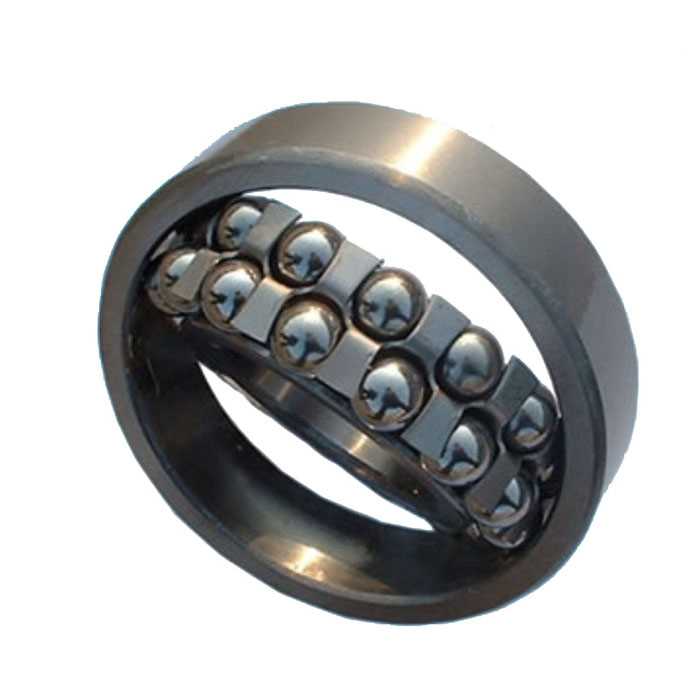
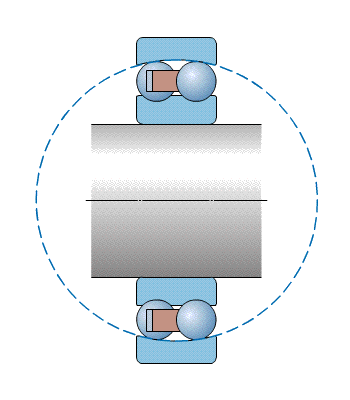
(a) Externally self-aligning bearing
In an externally self-aligning bearing, the outside diameter of the outer race is ground to a spherical surface which fits in a mating spherical surface in a housing.
(b) Internally self-aligning bearing.
In case of internally self-aligning bearing, the inner surface of the outer race is ground to a spherical surface.
(b) Thrust Ball Bearing
The thrust ball bearings are used for carrying thrust loads exclusively and at speeds below 2000 r.p.m. At high speeds, centrifugal force causes the balls to be forced out of the races. Therefore at high speeds, it is recommended that angular contact ball bearings should be used in place of thrust ball bearings.A thrust ball bearing may be a single direction, flat face or a double direction with flat face.
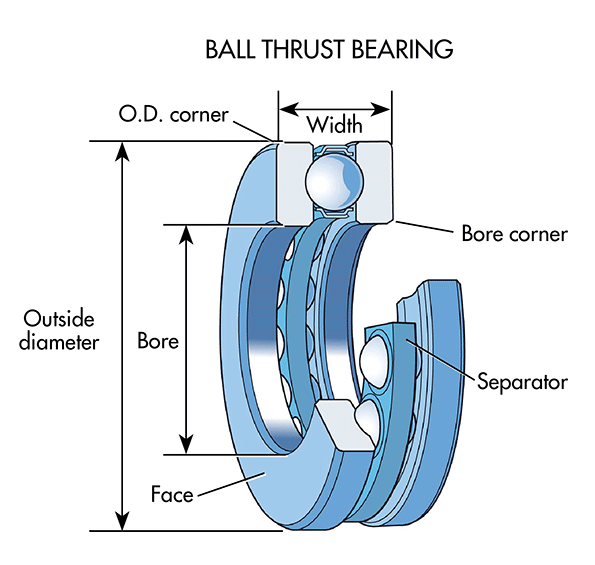
(2) Roller Bearing
(a) Radial Roller Bearing
(i) Cylindrical roller bearings
These bearings have short rollers guided in a cage. These bearings are relatively rigid against radial motion and have the lowest coefficient of friction of any form of heavy duty rolling-contact bearings. Such type of bearings are used in high speed service.
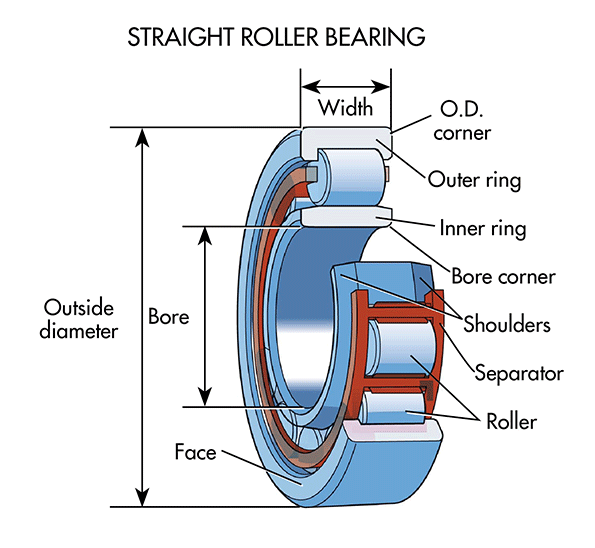

(ii) Spherical roller bearings
These bearings are self-aligning bearings. The self-aligning feature is achieved by grinding one of the races in the form of sphere. These bearings can normally tolerate angular misalignment in the order of ± 1.5 ° and when used with a double row of rollers, these can carry thrust loads in either direction.
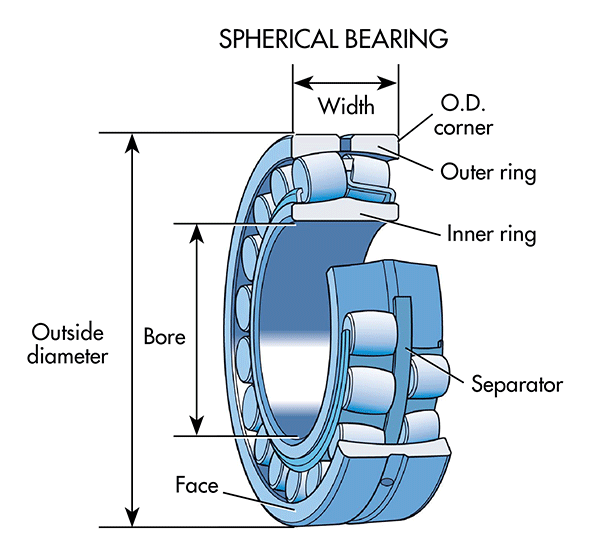

(iii) Needle roller bearings
These bearings are relatively slender and completely fill the space so that neither a cage nor a retainer is needed. These bearings are used when heavy loads are to be carried with an oscillatory motion, e.g. piston pin bearings in heavy duty diesel engines, where the reversal of motion tends to keep the rollers in correct alignment.
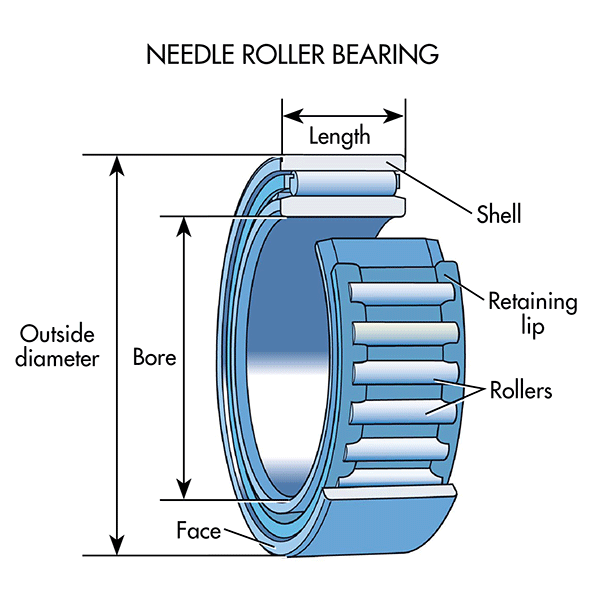

(iv) Tapered roller bearings
The rollers and race ways of these bearings are truncated cones whose elements intersect at a common point. Such type of bearings can carry both radial and thrust loads. These bearings are available in various combinations as double row bearings and with different cone angles for use with different relative magnitudes of radial and thrust loads.
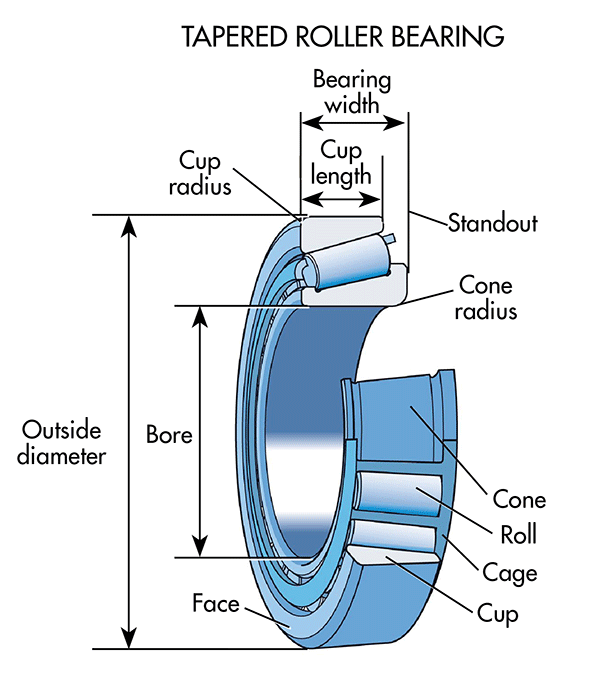

(b) Thrust Roller Bearing
When a roller bearing supports only a thrust load is to shift the plane of rotation of the rollers.
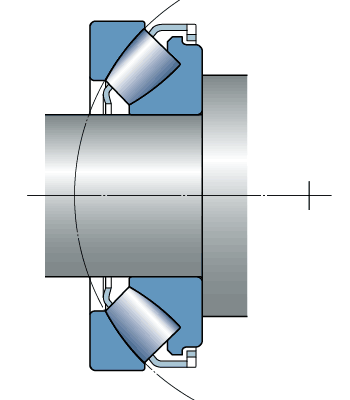
3. Depending upon the Materials
(a) Metallic Bearings
Metallic Bearing are generally made of metals. Ex- Cast Iron, Alloy Steels, Copper, Silver etc.
(b) Non Metallic Bearings
Non-Metallic Bearing are generally made other than metals. Ex- Rubber, Plastics, wood etc.
4. Depending upon the type of loading
(a)Bearing with Steady load
Such types of bearings used in Electric generators & motors, Centrifugal pumps or various blower & fans. Such bearings also called Power Bearings.
(b) Bearing with a variable or fluctuating load
Such types of bearings used in crankpin, wrist pin or camshaft of engines.
Comments
Post a Comment