Reciprocating Pump
Reciprocating Pump
"Reciprocating pump is a hydraulic machine which converts the mechanical energy into hydraulic energy."
It does this work by sucking liquid into a cylinder containing a reciprocating piston which exerts a thrust force on the liquid and increases its hydraulic energy ( pressure energy of liquid). It is a type of positive displacement pump which consists of piston or plunger. Piston is present in a cylinder in which it does reciprocating motion. It is used at a place where relatively small amount of water is to be delivered at higher pressure.

Main Parts of the Reciprocating Pump-
1. Cylinder & Piston
2. Crank & Connecting Rod
3. Suction pipe,
4. Delivery pipe,
5. Suction valve & Delivery valve
6. Air vessel.
3. Suction pipe,
4. Delivery pipe,
5. Suction valve & Delivery valve
6. Air vessel.
The main parts of a reciprocating pump is as follows:
1. Cylinder and piston: Reciprocating pump consists of a piston and cylinder arrangement. Piston moves to and fro in the cylinder i.e. piston reciprocates inside the cylinder that’s why it is known as reciprocating pump. Piston and cylinder is generally made up of cast iron or steel alloy.
2. Crank and connecting rod: Piston is connected to crank by means of connecting rod. Crank is driven by some external source like some engines or electric motor. Crank rotates at uniform speed. The connecting rod attached with piston and crank; which converts rotary motion of crank into reciprocating motion of piston i.e. piston moves in to and fro motion when crank is rotating.
3.Suction pipe: Suction pipe is connected to cylinder and source of water. It transfers water from source to cylinder.
4. Delivery pipe: Delivery pipe attached with cylinder to delivery end. Water is delivered through this delivery pipe.
5. Suction and delivery valves: Suction and delivery both the pipes are provided with one way or non returning suction and delivery valves. These valves permits entry and exit of water in one direction only i.e. suction valves allows the liquid to entry into the cylinder only and delivery valve permits only delivery/ discharge of liquid from the cylinder. We can also call them input and output valves.
6. Air vessels: Air vessels mostly use in case of single acting reciprocating pump. It is used to obtain continuous supply of liquid at a uniform rate from a single acting pump and it helps to maintain uniform rate of flow of liquid in both cases i.e. suction and delivery. Air vessel is a close chamber generally made up of cast iron and having an opening at its base through which the liquid flow out from the vessel. In air vessel top portion is filled with compressed air and at bottom some amount of liquid is present.
1. Cylinder and piston: Reciprocating pump consists of a piston and cylinder arrangement. Piston moves to and fro in the cylinder i.e. piston reciprocates inside the cylinder that’s why it is known as reciprocating pump. Piston and cylinder is generally made up of cast iron or steel alloy.
2. Crank and connecting rod: Piston is connected to crank by means of connecting rod. Crank is driven by some external source like some engines or electric motor. Crank rotates at uniform speed. The connecting rod attached with piston and crank; which converts rotary motion of crank into reciprocating motion of piston i.e. piston moves in to and fro motion when crank is rotating.
3.Suction pipe: Suction pipe is connected to cylinder and source of water. It transfers water from source to cylinder.
4. Delivery pipe: Delivery pipe attached with cylinder to delivery end. Water is delivered through this delivery pipe.
5. Suction and delivery valves: Suction and delivery both the pipes are provided with one way or non returning suction and delivery valves. These valves permits entry and exit of water in one direction only i.e. suction valves allows the liquid to entry into the cylinder only and delivery valve permits only delivery/ discharge of liquid from the cylinder. We can also call them input and output valves.
6. Air vessels: Air vessels mostly use in case of single acting reciprocating pump. It is used to obtain continuous supply of liquid at a uniform rate from a single acting pump and it helps to maintain uniform rate of flow of liquid in both cases i.e. suction and delivery. Air vessel is a close chamber generally made up of cast iron and having an opening at its base through which the liquid flow out from the vessel. In air vessel top portion is filled with compressed air and at bottom some amount of liquid is present.

Classification of the Reciprocating Pump-
Reciprocating pump may be classified in two ways
1. According to the contact of liquid with piston:
It can be one side or both side i.e. single acting pump and double acting pump.
(a) Single acting pump: As name suggest if the liquid is contact with the piston in one side and having only one suction and one delivery pipe then it is known as single acting pump. In single acting pump one crank revolution have only two strokes i.e. one is suction and second is delivery stroke.
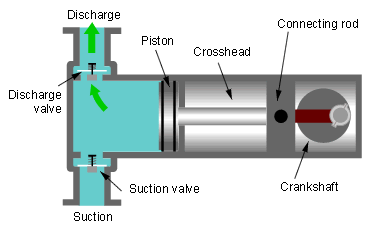
(b) Double acting pump: In this type water comes in contact with the piston on both the sides and having two suction and two delivery pipes with attached valves. In double acting pump in each stroke from one side suction and other side delivery takes place. In this manner double acting pump has two suctions and two delivery stroke in one complete revolution of the crank.

2. According to number of cylinders provides:
1. Single cylinder pump: As name suggests a single cylinder pump have only one cylinder, this can be single acting or may be double acting as per the requirement.

2. Double cylinder pump: A double cylinder pump has two possibilities i.e. having two cylinders with two separate pistons and having two cylinders in line but with single piston.
3.Triple cylinder pump: This is also known as three throw pump. In this type three cylinder having three separate pistons works together, all the three cylinders have separate delivery and suction pipes with appropriate valves. All three pistons moves together from a crank set angle of 120 degree.

4. Duplex cylinder pump: This is also known as four throw pump. In this case two double acting single cylinder pumps or may be two double acting double cylinder pumps are arranged. This arrangement is works with two cranks, each piston cylinder arrangement have separate crank with a set of 90 degree angles.

5. Quintuplex pump: It is also known as five throw pump. It has five single acting cylinders driven by cranks at 72 degree. The entire cylinder has their separate suction and delivery pipes with appropriate valves.
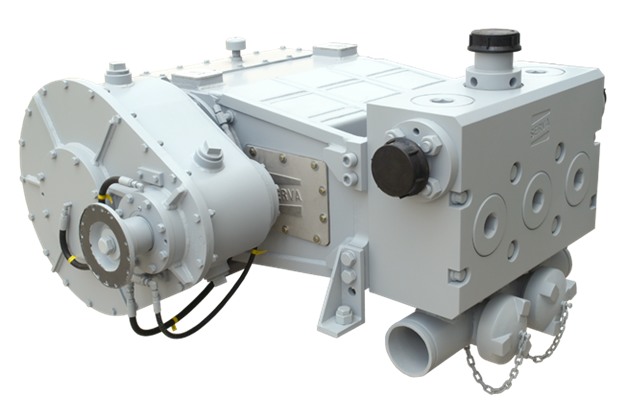
Working of the Reciprocating Pump-
Working of reciprocating pump is very simple. It works like a reciprocating engine. When crank starts rotates from 0 degree to 180 degree then the piston moves from extremely inward position to outward position, this time a partial vacuum is created in the cylinder i.e. pressure in the cylinder is slightly less than the atmospheric pressure. Due to this suction generates into the suction pipe this time suction valve is open and delivery valve is closed. The liquid comes into the cylinder fill into the cylinder. This is known as suction stroke. In starting of this stroke crank angle is 0 degree and at the end of this stroke crank angle is 180 degree. This time suction valve is closed and delivery valve is just about to open.
When crank rotates inward from 180 degree to 360 degree the piston moves inward from outward. This movement causes the pressure increase into the cylinder above the atmospheric pressure. This time suction valves close and delivery valves opens. The liquid forcefully pressed and delivered at required portion or height. This is known as delivery stroke. In both the strokes a complete revolution of crank is done. This process is continuously repeated and the delivery of liquid is done continuously.
Work done by Reciprocating Pump-
Let D= Diameter of the cylinder
A= Cross sectional area of the piston
r= Radius of crank
N= r.p.m of Crank
L= Length of stroke = 2 × r
hs= Height of axis of the cylinder from water surface in sump.
hd= Height of delivery outlet above the cylinder axis ( also called delivery head)
3. It is used to deliver the liquid at high heads.
4. Reciprocating pumps are highly durable i.e. can be use in adverse conditions like in corrosive applications.
5. It can works for air as well as with liquids.
3. These pumps require high maintenance sometimes wear and tears happen in it, in adverse operating conditions.
4. Reciprocating pumps are heavy and large in size.
A= Cross sectional area of the piston
r= Radius of crank
N= r.p.m of Crank
L= Length of stroke = 2 × r
hs= Height of axis of the cylinder from water surface in sump.
hd= Height of delivery outlet above the cylinder axis ( also called delivery head)
Volume of water deliver in one revolution = Area × Length of Stroke = A × L
Number of revolution per second = N/60
Discharge of pump per second = Discharge in one revolution x No. of revolution per second
= A × L × N / 60 = ALN/60
Weight of water delivered per second = W = r ×
g × Q
= rgALN / 60
Work done by Reciprocating Pump-
The work done by the reciprocating pump per second = Weight of water lifted per second × Total height through which water is lifted
= W × (hs + hd)
We Know W = r × g × Q = rgALN / 60
Work done per second = (rgALN / 60) × (hs + hd)
Power Required to drive the pump in KW
P = Work done per second / 1000
P = [rgALN × (hs + hd)] / 60000 KW
P = Work done per second / 1000
P = [rgALN × (hs + hd)] / 60000 KW
Slip of the Reciprocating Pump-
Slip in reciprocating pump is the measure of "difference between theoretical discharge and actual discharge."
Slip = Qth - Qact
Percentage of slip= (Qth- Qact) *100% / Qth = (1-Cd)*100%
where Cd is Co-efficient of discharge.
When actual discharge delivered by reciprocating pump is less than theoretical discharge then that difference is called as Positive Slip.
And when actual discharge delivered by reciprocating pump is more than theoretical discharge then that difference is called as Negative Slip.Negative slip occurs when delivery pipe is short, suction pipe is long and pump is running at high speed.
Separation: if cylinder pressure is less than the vapor pressure of liquid then the dissolved gases liberated from the liquid and cavitation takes place. As a result continuous flow of liquid does not exist and it is called separation.
Advantages of the Reciprocating Pump-
1. The main advantage of reciprocating pump is there is no requirement of priming in it as it is positive displacement pump.
2. It can be used for supply liquid at high pressure.3. It is used to deliver the liquid at high heads.
4. Reciprocating pumps are highly durable i.e. can be use in adverse conditions like in corrosive applications.
5. It can works for air as well as with liquids.
Disadvantages of the Reciprocating Pump-
1. The major drawback of this pump is its lower efficiency as compared to centrifugal pumps.
2. Reciprocating pumps have low discharge.3. These pumps require high maintenance sometimes wear and tears happen in it, in adverse operating conditions.
4. Reciprocating pumps are heavy and large in size.
Applications of the Reciprocating Pump-
1. Reciprocating pump used in water jet cutting, where high pressurized liquid is required at high velocity.
1. Reciprocating pump used in water jet cutting, where high pressurized liquid is required at high velocity.
2. It is widely used in oil and gas industries, power plants, water treatment plants and sugar industries.
3. These pumps use where low discharge is required at high presser.
4. Reciprocating pump is used to fill air into the tires of bike or bicycles.
5. The most important and common use of reciprocating pump as hand pump.
3. These pumps use where low discharge is required at high presser.
4. Reciprocating pump is used to fill air into the tires of bike or bicycles.
5. The most important and common use of reciprocating pump as hand pump.
Comments
Post a Comment