Two Stroke Engine
Two Stroke Engine
A two-stroke (or two-cycle) engine is a type of internal combustion engine which completes a power cycle with two strokes (up and down movements) of the piston during only one crankshaft revolution.
In a two-stroke engine, the end of the combustion stroke and the beginning of the compression stroke happen simultaneously, with the intake and exhaust (or scavenging) functions occurring at the same time.
Two-stroke engines often have a high power-to-weight ratio, power being available in a narrow range of rotational speeds called the "power band".
History
The first commercial two-stroke engine involving in-cylinder compression is attributed to Scottish engineer Dugald Clerk, who patented his design in 1881. However, unlike most later two-stroke engines, his had a separate charging cylinder. The crankcase-scavenged engine, employing the area below the piston as a charging pump, is generally credited to Englishman Joseph Day. On 31 December 1879, German inventor Karl Benz produced a two-stroke gas engine, for which he received a patent in 1880 in Germany. The first truly practical two-stroke engine is attributed to Yorkshireman Alfred Angas Scott, who started producing twin cylinder water cooled motorcycles in 1908.
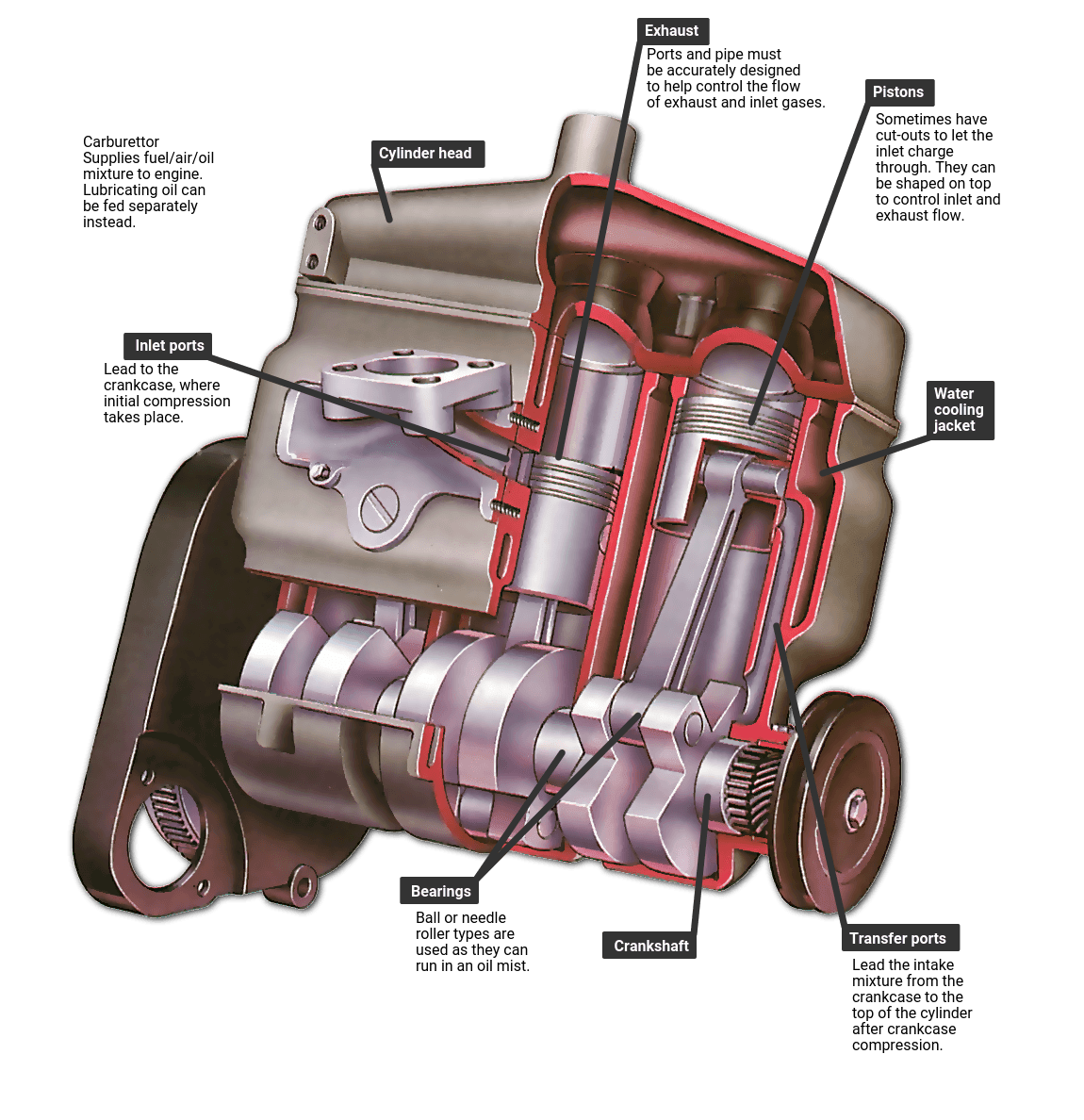
Part's of Two Stroke Engine
The parts which a 2 stroke engine has –
1. Cylinder- The cylinder are made of cast iron for withstanding the high pressure & temperature inside the cylinder.
2. Cylinder Head- It's the top most portion of the cylinder & houses of spark plug for petrol engine & fuel injector for diesel engine. The engine head made of cast iron.
3. Piston – In an engine, piston is used to transfer the expanding force of gases to mechanical rotation of crankshaft via a connecting rod. The piston is able to do this because it is secured tightly within cylinder using piston rings to minimize the clearance between cylinder and piston.
4. Crankshaft – A crankshaft is a part which is able to convert the reciprocating motion to rotational motion.
5. Connecting rod – A connecting rod transfers motion from a piston to crankshaft which acts as a lever arm.
6. Crankcase- It's the house of crank, crankshaft, lubricating oil & other fastened engine parts. Generally the crankcase made of cast iron or cast aluminium by the method of sand casting.
7. Counterweight – Counterweight on crankshaft is used to reduce the vibrations due to imbalances in the rotating assembly.
8. Flywheel – Flywheel is a rotating mechanical device which is used to store energy.
9. Ports- Ports are generally used in two stroke engines for inlet charge & exhaust gases. There are three types of port in two stroke engine-
1. Inlet Port - It allows to enter fresh air with fuel.
2. Transfer Port- This port are used for transfer the charges.
3. Outlet or Exhaust Port- The waste gases are exits from this port.
10. Spark Plug (For Petrol Engine) – A spark plug delivers electric current to the combustion chamber which ignites the air-fuel mixture leading to abrupt expansion of gas.
11. Fuel Injector ( For Diesel Engine) - A fuel injector inject the fuel during end of compression stroke in diesel engine with the help of pump.
Types of Two Stroke Engine
Two stroke engine are two types
1. Two Stroke Petrol Engine
2. Two Stroke Diesel Engine
Working of Two Stroke Petrol Engine
There are two Stroke in Petrol Engine
1. First Stroke (Suction & Compression Stroke)- During the first stroke, the piston moves from Bottom Dead Centre (BDC) to Top Dead Centre (TDC), compressing the air-petrol mixture in the cylinder. The cylinder is connected to a closed crank chamber. Due to upward movement of the piston, a partial vacuum is created in the crankcase, and a new charge is drawn into the crankcase through the uncovered inlet port. The exhaust port and transfer port are covered when the piston is at the top dead Centre position. The compressed charge is ignited in the combustion chamber by a spark provided by the spark plug.
2. Second Stroke (Working & Exhaust Stroke)-During Second stroke the charge is ignited, the hot gases force the piston to move downwards, rotating the crankshaft, thus doing the useful work. During this stroke the inlet port is covered by the piston and the new charge is compressed in the crank case. Further downward movement of the piston uncovers first the exhaust port and then the transfer port. The burnt gases escape through the exhaust port. As soon as the transfer port opens, the compressed charge from the crankcase flows into the cylinder. The charge is deflected upwards by the pump provided on the head of the piston and pushes out most of the exhaust gases. It may be noted that the incoming air-petrol mixture helps the removal of burnt gases from the engine cylinder, which is called as the scavenging process. If in case these exhaust gases do not leave the cylinder, the fresh charge gets diluted and efficiency of the engine will decrease. The cycle of events is then repeated.
Working of Two Stroke Diesel Engine
In a two stroke cycle diesel engine, only air is compressed inside the cylinder and the diesel is injected by an injector. There is no spark plug in this engine. The remaining operations of the two stroke cycle diesel engine are exactly the same as those of the two stroke cycle petrol engine. Its two strokes are described as follows:
1. First Stroke (Suction & Compression Stroke): During the First stroke, the piston moves from bottom dead Centre to top dead Centre, compressing the air in the cylinder. The cylinder is connected to a closed crank chamber. Due to upward movement of the piston, a partial vacuum is created in the crankcase, and a new charge is drawn into the crankcase through the uncovered inlet port. The exhaust port and transfer port are covered when the piston is at the top dead Centre position. The compressed charge is mixed with the injected diesel and gets auto-ignited in the combustion chamber because of the high pressure and temperature present.
2. Second Stroke (Working & Exhaust Stroke)-: During the second stroke the fuel is ignited, the hot gases force the piston to move downwards, rotating the crankshaft, thus doing the useful work. During this stroke the inlet port is covered by the piston and the new charge is compressed in the crank case. Further downward movement of the piston uncovers first the exhaust port and then the transfer port. The burnt gases escape through the exhaust port. As soon as the transfer port opens, the compressed charge from the crankcase flows into the cylinder. The charge is deflected upwards by the pump provided on the head of the piston and pushes out most of the exhaust gases. It may be noted that the incoming air helps the removal of burnt gases from the engine cylinder, which is called as scavenging process. If in case these exhaust gases do not leave the cylinder, the fresh charge gets diluted and efficiency of the engine will decrease. The cycle of events is then repeated.
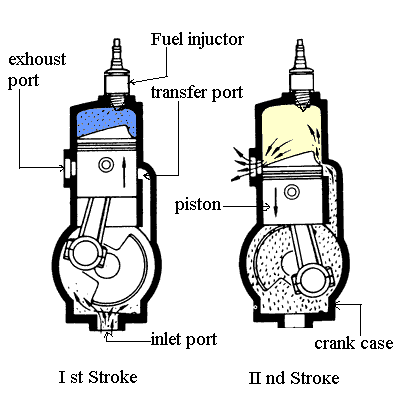
Two Stroke Valve Timing Diagram for Petrol Engine
1. First of all, the exhaust port opens a fraction of the crank revolution, the transfer port also opens and the fresh fuel-air mixture enters into the engine cylinder. This is done as the fresh incoming charge helps in pushing out the burnt gases.
2. The piston reaches BDC and then starts moving upwards. As the crank moves a little beyond BDC, first the transfer port closes and then the exhaust port also closes. This is done to suck fresh charge through the transfer port and to exhaust the burnt gases through the exhaust port simultaneously.
3. The charge is compressed with both ports closed and then ignited with the help of a spark plug before the end of the compression stroke. This is done as the charge requires some time to ignite. By the time the piston reaches TDC, the burnt gases (under high pressure and temperature) push the piston downwards with full force, and the expansion of the burnt gases takes place.
It may be noted that the exhaust and transfer ports open and close at equal angles on either side of the BDC position.
Two Stroke Valve Timing Diagram for Diesel Engine
1. First of all, the exhaust port opens before the piston reaches BDC and the burnt gases start leaving the cylinder. After a small fraction of the crank revolution, the transfer port also opens and the fresh air enters into the engine cylinder. This is done as the fresh incoming air helps in pushing out the burnt gases.
2. Now the piston reaches BDC and then starts moving upwards. As the crank moves a little beyond BDC, first the transfer port closes and then the exhaust port also closes. This is done to suck fresh air through the transfer port and to exhaust the burnt gases through the exhaust port simultaneously.
3. Now the charge is compressed with both the ports closed. The fuel valve opens a little before the piston reaches the TDC.
4. Now the fuel is injected in the form of very fine spray into the engine cylinder, which gets ignited due to the high temperature of the compressed air. The fuel valve closes after the piston has come down a little from the TDC. ‘This is done as the required quantity of fuel is injected into the engine cylinder.
5. Now the burnt gases (under high pressure and temperature) push the piston downwards with full force and expansion of the gases takes place. It may be noted that in a two-stroke cycle diesel engine, like a two-stroke petrol engine, the exhaust and transfer ports open and close at equal angles on either side of the BDC position.
Advantages of Two Stroke Engine
1. Two stroke engines do not have valves which are easy to construct and lowers their weight
2. Two stroke engines fire once every revolution. Power is produced once during Two strokes of the piston .This gives a significant power boost.
3. This two stroke engines lower output in horse power.
4. Two stroke engines can work in any position, since oil flow is not a concern with any valves to worry about
5. Two stroke engines are lighter comparatively.
6. Since the power produced by the two-stroke engine is higher, these engines are small and compact in size.
7. The torque produced on the crankshaft is more uniform because the power is produced during every alternate stroke of the piston.
8. These Engines often provide high power-to-weight ratio, usually in a narrow range of rotational speeds called the “power band”.
Disadvantages of Two Stroke Engine
1. Two stroke engines do not last as long as four stroke engines; there is no lubrication system in a two stroke engine so parts wear out a lot faster.
2. Two stroke use more fuel.
3. Two stroke engines are Less Efficient.
4. Two stroke engines produce a lot of pollution, and the way the engine is designed that part of the air/fuel leaks out of the chamber through the exhaust port.
5. The exhaust gases often get trapped inside the combustion chamber. This makes the fresh charge impure. Therefore maximum power doesn’t get delivered because of improper incomplete combustion.
6. Since in two-stroke engines power stroke is produced after every stroke, a large amount of heat is generated within them. To reduce the temperature of the engine and keep the moving parts well-lubricated, good lubrication and cooling systems for the engine are required.
Application of Two Stroke Engine
There are many motorcycle /Scooter which run on two stroke engine. These are-
1. Yamaha RX135/RX-z
2. Kinetic Honda
3. Kawasaki-Bajaj Enduror
4. Bajaj Chetak
5. Suzuki Shogun
6. Suzuki Shaolin
7. Yezdi Roadking 250
8. Yezdi 350
Comments
Post a Comment